Geschichten aus der Fertigung #04
ROHMs einzigartige "Stärken"
in "Vertrauen" umwandelnProzess der Waferherstellung
Kern-Produktionsstätte für Analoge Ics
In Hamamatsu herrscht ein mildes Klima, es ist bekannt für seine Textilindustrie, die seit der Edo-Zeit fortbesteht, sowie für seine Musikinstrumente, Motorräder und andere namhafte Produktionsunternehmen.
ROHM Hamamatsu, Co., Ltd. nahm 1999 den Betrieb als Kern-Produktionsstätte auf, das für die Front-End-Verarbeitung von ROHM-ICs und -LEDs zuständig ist. Im Laufe der Jahre hat ROHM Produkte auf den Markt gebracht, die auf den Bedarf der Zeit zugeschnitten sind. Wir haben schnell auf die Entwicklung des digitalen Marktes, die Globalisierung des Marktes und hin zu einer kohlenstoffarmen, recyclingorientierten Gesellschaft reagiert.
ROHM Hamamatsu verfügt über fortschrittliche Bauteil- und Prozesstechnologien und Produktionsanlagen, die auf analoge ICs spezialisiert sind, und produziert mehr als 70 % der von ROHM hergestellten ICs.
Das Werk hat zwei Produktionslinien für 8- und 12-Zoll-Wafer und hat eine monatliche Produktionskapazität von mehr als 50.000 Wafern (*8-Zoll-Äquivalent).
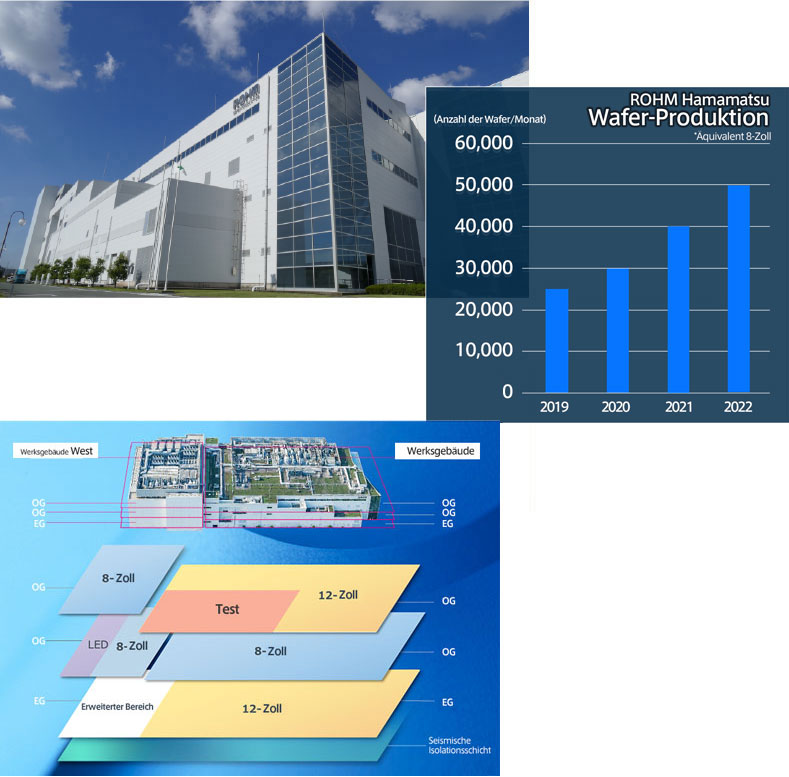
ROHM Hamamatsu Co., Ltd. (Hamamatsu-Stadt, Präfektur Shizuoka)
Besteht aus zwei Fabrikgebäuden auf einem Gelände von etwa 62.000 m2.
Die weltweit erste Halbleiterfabrik, die eine seismisch isolierte Struktur verwendet.
Die Gesamtfläche beträgt ca. 30.000 m2. Ein ca. 160 m langer Gang führt zwischen den Reinräumen und dem westlichen Fabrikgebäude mitten durch die Fabrik. Hier werden mehr als 1.000 verschiedene ICs hergestellt.
Das komplexe Produktionssystem, das neben der Massenproduktionslinie auch mehrere Produktionslinien umfasst, ermöglicht eine "High-Mix-High-Volume-Produktion".
ROHM reagiert somit auf ein breites Spektrum von Kundenwünschen.
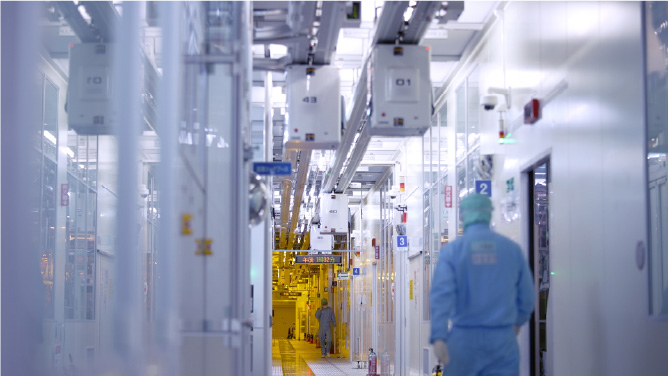
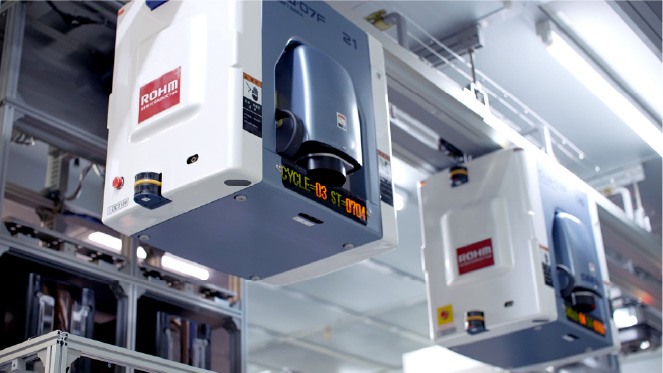
Pods mit 24 12-Zoll-Wafern durchqueren auf Schienen über Kopf den Reinraum.
Von der Verladung bis zum Versand legen sie durchschnittlich 25 km zurück.
Die Entwicklung der Mobilitätsgesellschaft
Gegenwärtig sind die Produkte für die Automobilindustrie die wichtigsten Produkte in der Produktionspalette von ROHM Hamamatsu. ROHM Hamamatsu ist seit seiner Gründung im Jahr 1999 in diesem Bereich tätig und hat nach und nach das Vertrauen der Kunden gewonnen, so dass Automobilprodukte heute 60 % der Gesamtproduktion ausmachen.
Die Umstellung auf EVs und HEVs, die weit verbreitete Einführung von ASVs (Advanced Safety Vehicles) und der Entwicklung des autonomen Fahrens hat zu einem enormen Anstieg der Anzahl elektronischer Bauteile geführt. Es wird erwartet, dass die Nachfrage nach Automobilprodukten weiterhin stark ansteigen wird.
Die Standards für Produktsicherheit und Zuverlässigkeit bei Automobilprodukten sind verständlicherweise sehr streng, um die Sicherheit des Enderverbrauchers zu gewährleisten (z.B. AEC-Q100, IATF 16949, ISO 26262).
ROHM Hamamatsu hat über viele Jahre hinweg mehr als 3 Milliarden ICs an Kunden weltweit geliefert. Dies ist ein Beweis für unsere gründliche Qualitätskontrolle und unsere Fähigkeit, die strengsten Normen zu erfüllen.
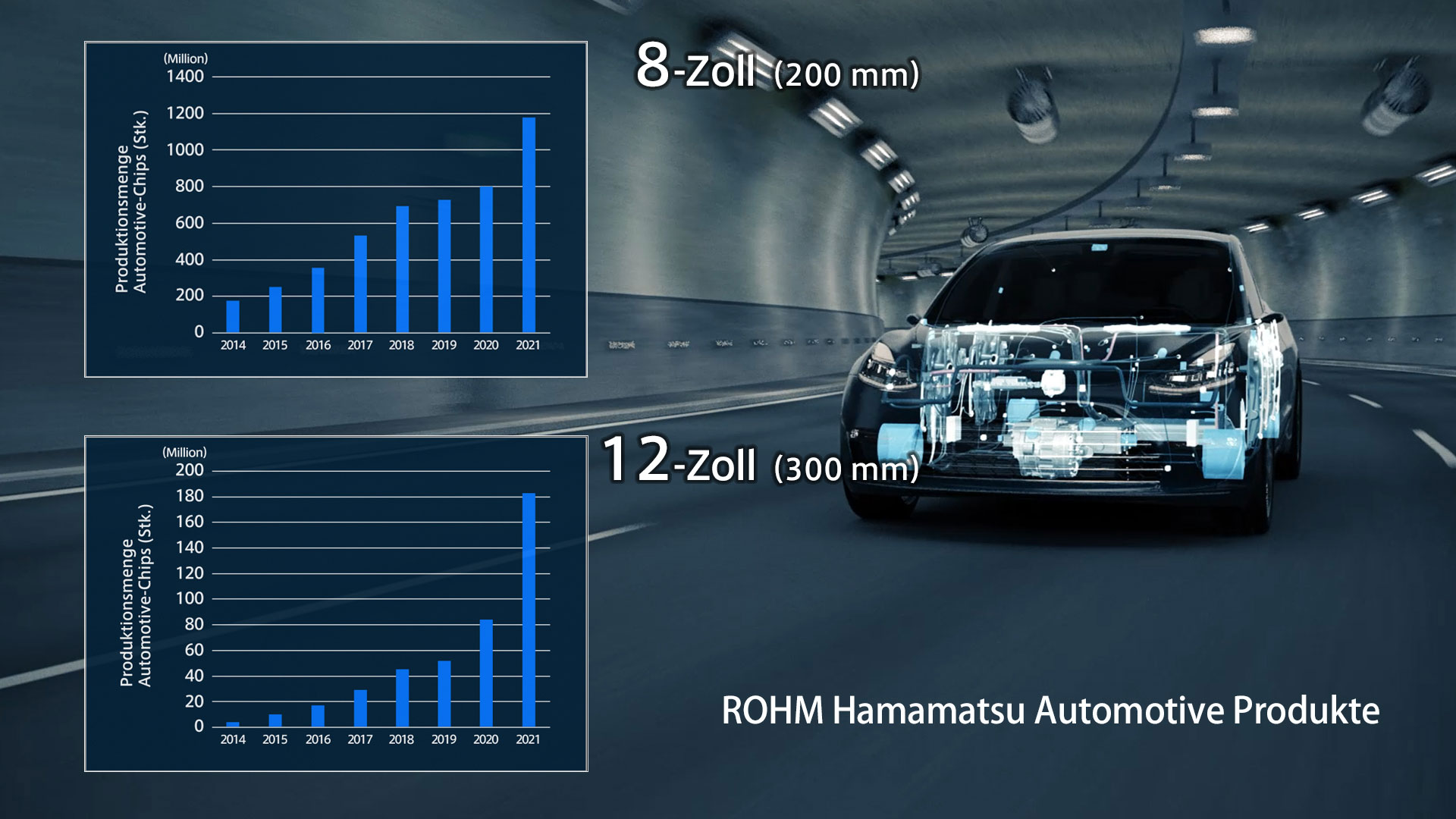
ROHM Hamamatsu's Produktionsergebnisse im Automotive-Bereich
Die Anzahl der produzierten Chips im Jahr 2021 umfasst ca. 1,4 Milliarden
Sie hat sich von 2014 bis 2021 versiebenfacht.
Dies ist kein Markt, auf dem die bloße Erfüllung der geforderten Spezifikationen ausreicht.
Die Frage, wie es dem Unternehmen gelang, das Vertrauen der Kunden zu gewinnen beantwortete Herr Yamashita von der 1st Manufacturing Dept., LSI Production Division.
Herausforderungen auf dem Weg zu 12-Zoll (300mm) BiCDMOS
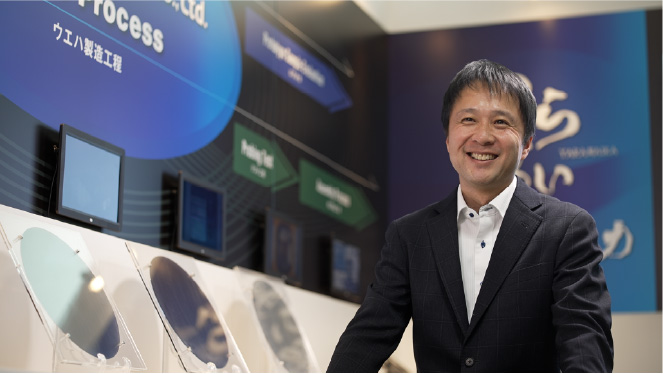
ROHM Hamamatsu Co., Ltd.
Manufacturing Div.1, LSI Manufacturing Headquarters
Er begann seine Karriere bei ROHM Hamamatsu auf dem Einstiegslevel: "Was ist ein Halbleiter?"
Heute ist er dankbar für ein Umfeld, das seine Selbstverwirklichung gefördert hat.
Eigene Kapazitäten zur Unterstützung von Innovationen
ROHM hat den 12-Zoll-BiCDMOS-Prozess in Angriff genommen, der bis dahin noch von keinem großen globalen Unternehmen realisiert worden war.
Die firmeneigene Entwicklungstechnologie für Fertigungsanlagen wurde seit der Gründung des Unternehmens kontinuierlich weiterentwickelt. ROHM Hamamatsu hat eine einzigartige Produktionslinie geschaffen, die ein Gleichgewicht zwischen eigenen, prozessoptimierten Produktionsanlagen und zugekauften Anlagen herstellt, die in Zusammenarbeit mit Ingenieuren der Anlagenhersteller optimiert wurden.
Als die 12-Zoll-Produktionslinie eingeführt wurde, wurde der größte Teil der Ausrüstung intern entwickelt.
Herr Taniguchi, Equipment Engineering Section 1, Production Department 1, LSI Production Division, blickt auf diese Zeit zurück.
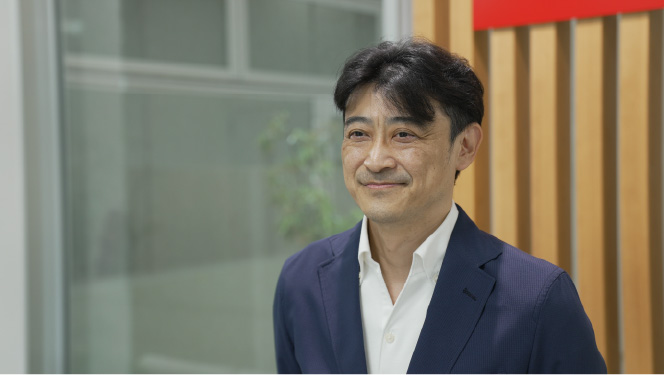
ROHM Hamamatsu Co., Ltd.
Equipment Engineering Dept.1, Manufacturing Div.1,
LSI Manufacturing Headquarters
Taniguchi:
„Die Hochtemperaturverarbeitung ist ein entscheidender Schritt im BiCDMOS-Wafer-Prozess, hierbei kam es aber unweigerlich zu Siliziumverformungen bei 12-Zoll-Wafern.
Durch eine Überarbeitung des Bauteildesigns des Wärmebehandlungsofens waren wir daher in der Lage, die Verarbeitung bei einer Ultrahochtemperatur von 1200℃ durchzuführen, die die allgemeine Hochtemperaturgrenze überschreitet.
Ingenieure geben ihr Wissen von Generation zu Generation weiter. Sie haben ein fundiertes Wissen über die Anlagen und den Waferprozess. Die Fähigkeit, Position und Ursache von Mängeln sofort zu erkennen, ist etwas, was man sich nicht von heute auf morgen aneignet."
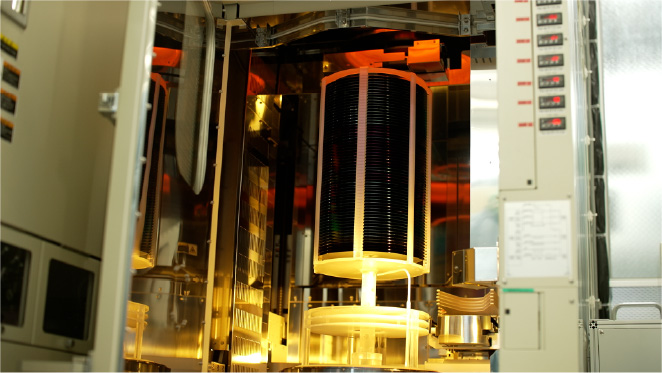
Ionenimplantierte Wafer in einem Ultrahochtemperatur-Wärmebehandlungsofen.
Die Verbesserung und Wartung der Produktionsanlagen hat großen Einfluss auf die Qualität der Wafer.
Wir legen besonderen Wert darauf, dass innerhalb des vertikal integrierten Produktionssystems alle Abteilungen zusammenarbeiten und dabei ihre Geräte, Prozesse und Anlagen bestmöglich nutzen, um Probleme gemeinsam zu lösen - dies ist eine von ROHM's Stärken.
Die Fähigkeiten vor Ort, verschiedene technische Herausforderungen zu meisten...
Dies ist vielleicht die größte Stärke von ROHM Hamamatsu.
Im Folgenden sind einige Beispiele, die dies belegen.
Frontloading und Qualitätssicherung
Isolierte Gate-Treiber-ICs dienen der Steuerung von Leistungsbauteilen, die für den Antrieb des Hauptmotors in EVs/HEVs verantwortlich sind. ROHM war 2016 das weltweit erste Unternehmen, das diese Produkte, die für die Mobilität der nächsten Generation als unverzichtbar gelten, in Massenproduktion herstellte, und hat seitdem den größten Marktanteil erobert.
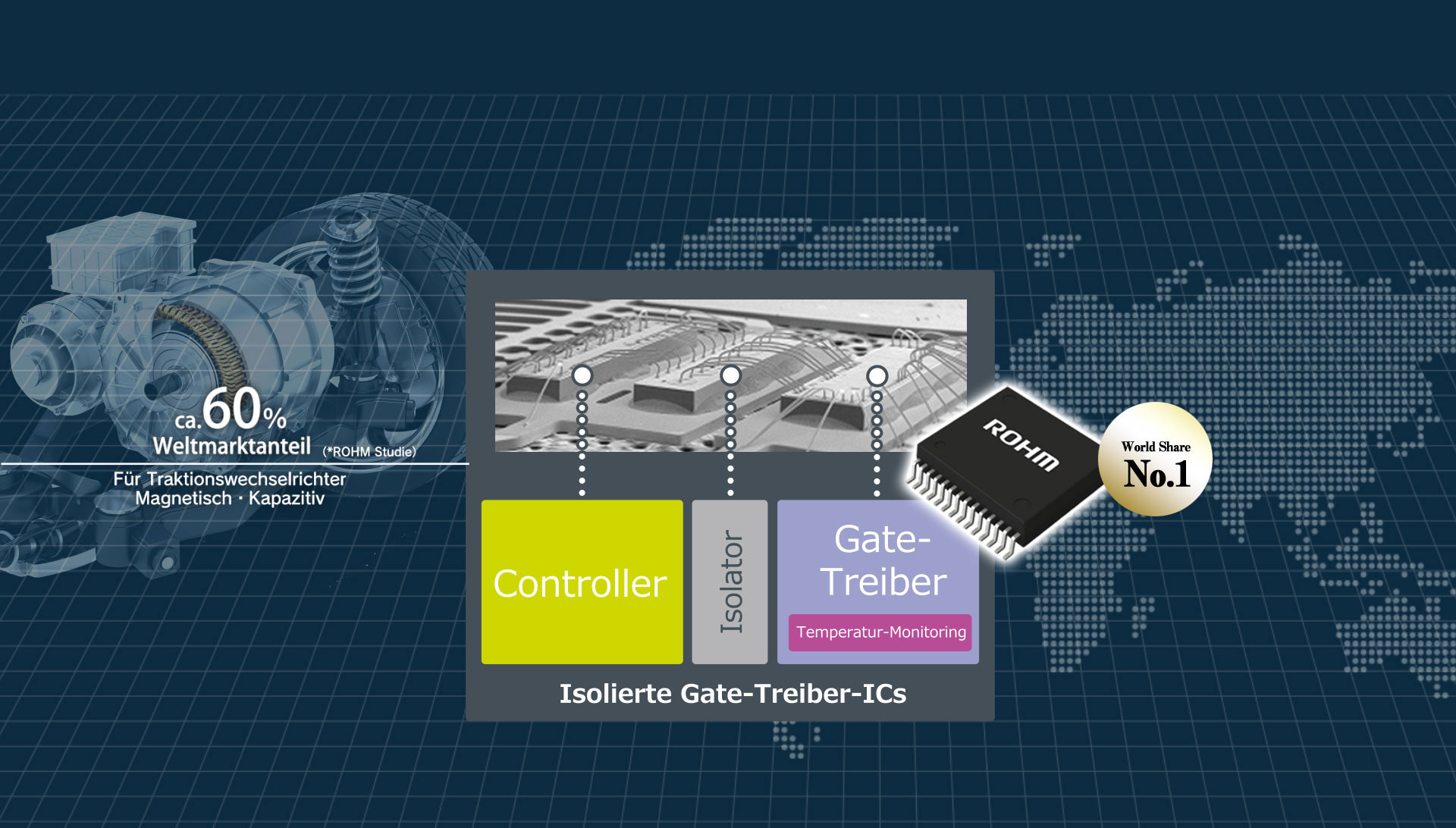
Durch die Verwendung eines magnetischen Verfahrens zur Isolierung anstelle eines optischen (Fotokoppler) wird eine bahnbrechende Miniaturisierung mit einem Single-Package-Design erreicht.
Es dauerte jedoch mehr als ein Jahr, um das Vertrauen der Kunden für dieses völlig neue Produkt zu gewinnen.
Herr Wada, Leiter der Technologieentwicklung bei ROHM LSI Business Div. und an dem Projekt beteiligt, teilt seine Gedanken mit.
Wada:
„Wir mussten ein hohes Risiko eingehen, da es sich um ein Automobil-Bauteil handelt, das das Herzstück des Hauptantriebsmotors bildet. Im Falle einer Fehlfunktion steht die Sicherheit des Endnutzers auf dem Spiel, so dass es notwendig war, die Qualität unter Berücksichtigung aller Risiken sicherzustellen."
Beispielhaft ist hier die Kontrolle von Fremdpartikel in der Produktion.
Bei ROHM Hamamatsu verfolgen wir den Plan "keine Fremdpartikel" z.B. in der Anlagenplanung, dem Anlagenmanagement, einschließlich der präventiven Instandhaltung und den Prozessbedingungen. Darüber hinaus ergreifen wir Maßnahmen zur Fehlervermeidung, wie z. B. Screening-Tests vor dem Produktversand.
„Was passiert, wenn Fremdpartikel enthalten sind?" und „Funktioniert das Screening wirklich wie in der Theorie vorgesehen?".
Das Video auf dieser Seite zeigt die Lösungsmöglichkeiten. Er teil seine Gedanken über die hier gewonnene Qualität.
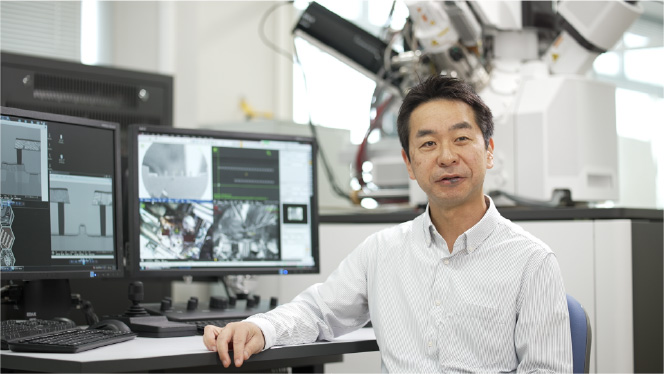
Process Development Dept., LSI Device Development Div.,
Technology Development Segment, LSI Business Unit
Wada:
„Zum einen war es ein gutes Erlebnis zu erfahren, wie wichtig es ist, Qualität zu gewährleisten. Neben der Qualitätssicherung, die wir durch den Frontloading-Prozess aufgebaut haben, müssen wir auch das Risiko mit Blick auf die Zukunft managen.
Und zum anderen die Technologie und das System zur Lösung aller Fragen und Probleme, die uns von Kunden erreichen.
Ich kann mit Stolz sagen, dass all dies zusammen 'unsere Qualität' ausmacht."
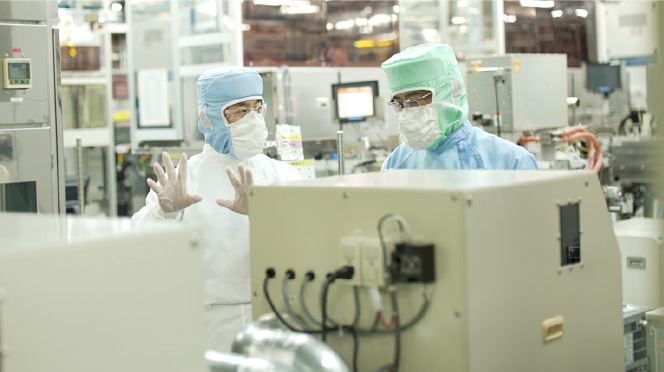
Um die Wirksamkeit des Screening-Tests zu demonstrieren, wurden über einen Zeitraum von mehreren Monaten absichtlich mit Fremdpartikeln versehene Wafer hergestellt.
Durch dieses Projekt ist allen Beteiligten im Unternehmen das Gewicht unserer sozialen Verantwortung in der Halbleiterherstellung einmal mehr bewusst geworden.
Herr Wada ist bei ROHM Hamamatsu in der Entwicklungsabteilung tätig und leitet ein Team von Ingenieuren, die sich auf Prozessdesign, Simulation, Maskendesign und Messungen/Analysen spezialisiert haben. Neben der Verbesserung der technischen Fähigkeiten seines eigenen Teams konzentriert er sich auch auf den „Aufbau enger Beziehungen" mit der für die Produktion und Ausrüstung zuständigen Abteilung.
Wada:
„Es ist ein Vorteil, dass unsere Abteilungen bei ROHM Hamamatsu räumlich nahe beieinander liegen. Wenn es Probleme mit einem Produkt gibt, das in Serie produziert wird, berät sich die Produktion mit uns und wir arbeiten gemeinsam an Lösungen.
Ich bin der Meinung, dass die räumliche Nähe sehr wichtig für die Verbesserung der Qualität ist."
Entwicklung und Produktion arbeiten zusammen, um Fragen und Bedenken der Kunden zu klären. Dies ist ein einzigartiger Vorteil des vertikal integrierten Produktionssystems von ROHM. Die „Stärke", die entsteht, wenn sich das Unternehmen in eine Richtung bewegt, führt zu „Vertrauen" beim Kunden.
Mehr als "Quality First"…
Yamashita:
„Neulich kam ein Kunde wegen eines Audits zur Einführung neuer Bauteile zu uns und erwähnte, dass Ehrlichkeit und Reaktionsfähigkeit die Gründe für die Wahl auf ROHM waren.
Er sagte, ROHMs Stärke ist die Zusammenarbeit mit dem Kunden, die Zuverlässigkeit Probleme anzugehen und zu lösen.
Damals hatte Herr Yamashita den Gedanken „Quality First", das heutige Unternehmensziel von ROHM.
Dies bedeutet nicht nur Produkte mit guten Eigenschaften zu liefern oder große Mengen guter Produkte herzustellen, sondern auch unsere Kunden und die Endverbraucher zufrieden zu stellen.
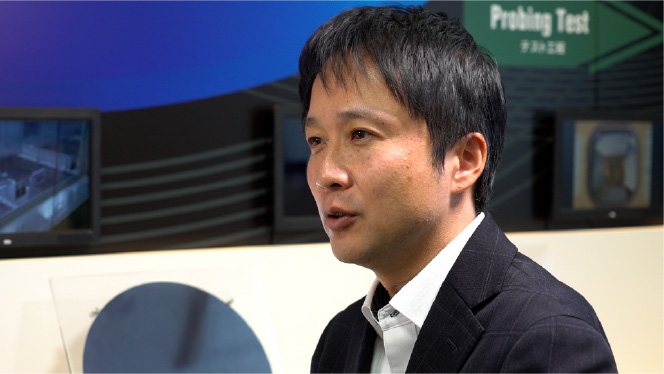
Ein Kunde sagte „Ehrlichkeit ist ROHMs Stärke". Das hat mich sehr beeindruckt und ich habe meinen Kollegen und Kolleginnen sofort davon berichtet.
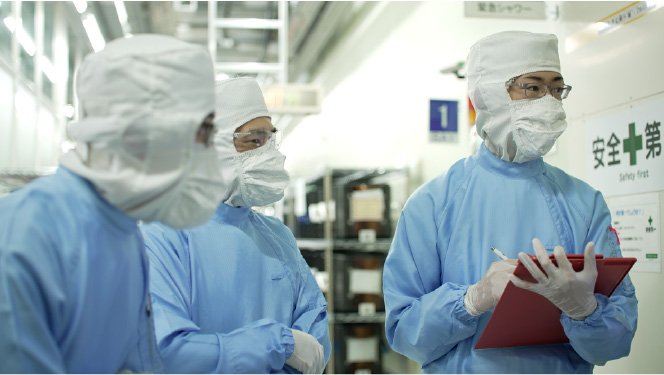
Etwa 800 Mitarbeiter arbeiten bei ROHM Hamamatsu. (*Stand: Mai 2023)
Ein Mantra Japans ist „Yaramaika!" - Dies bedeuet "Lasst es uns versuchen!".
Es ist nicht leicht, den Produktionsprozess völlig neu zu denken. Erlernte Abläufe zu hinterfragen, fällt schwer, wenn sich bereits eine gewisse Routine ergeben hat und klare Regeln und Vorgaben bestehen.
Für eine neue Welt mit Halbleitern der nächsten Generation
ROHM Hamamatsu erweitert derzeit die 12-Zoll-Linie, die im Juli 2023 in Betrieb gehen soll, um das Produktionsvolumen weiter zu erhöhen.
Darüber hinaus entwickelt ROHM als neue Technologie für die 12-Zoll-Linie schrittweise einen „Dickschicht-Cu-Verdrahtungsprozess", um den Marktanforderungen nach noch höherem Strom gerecht zu werden. Die Freigabe eines 0,13-µm-BiCDMOS mit DTI (Deep Trench Isolation) ist ebenfalls geplant..
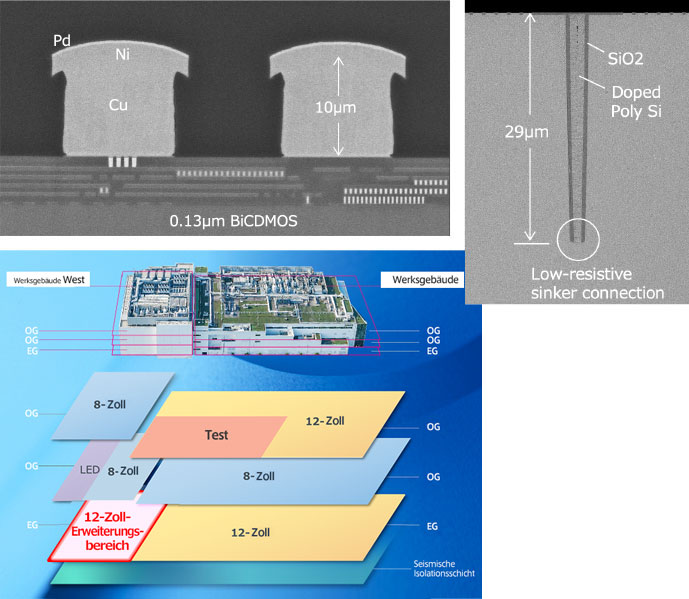
Dickschicht-Cu-RDL-Verfahren (Umverteilungsschicht)
DTI (Deep Trench Isolation)
Yamashita:
„Die Automobilbranche befindet sich mitten in einer technologischen Revolution. Wir haben es uns zur Aufgabe gemacht, jederzeit die von unseren Kunden geforderte Zuverlässigkeit und Qualität zu liefern - oder diese sogar zu übertreffen.
Wir hoffen, dadurch einen Beitrag zu einer neuen Welt mit Halbleitern der nächsten Generation leisten zu können, indem wir unsere Stärken mit den Stimmen unserer Kunden verbinden!"
Verwandte Links
ROHM Hamamatsu Co., Ltd. https://micro.rohm.com/en/hamamatsu/
Yamashita:
"Wir stellen uns seit über 20 Jahren immer wieder der Herausforderung, qualitätsorientiert zu produzieren, nicht nur im Bereich der Automobilindustrie. Ein Meilenstein war die weltweit erste Massenproduktion mit einem 12-Zoll-BiCDMOS-Prozess im Jahr 2009.