Geschichten aus der Fertigung #02
Als Vorreiter (in der Industrie),
was an sich schon eine Herausforderung warEntwicklung von flexiblen Anlagen
Aufbau der nächsten Generation von Produktionslinien
ROHMs Apollo-Werk in Hirokawa in der Präfektur Fukuoka hat eine neue Back-End-Prozesslinie für Halbleiter in Betrieb genommen. Die Musterproduktion begann im April 2021.Im darauf folgenden Jahr, 2022, begannen wir mit der Massenproduktion diskreter Produkte.
Der Reinraum, der das Konzept einer "unbemannten Produktionsanlage" verkörpert, zeichnet sich durch ein kompaktes Design mit drei U-förmig angeordneten Anlagen aus, zwischen denen AGVs (Automated Guided Vehicles) verkehren. Techniker überwachen den Status aller Produktionslinien über Monitore in einem angrenzenden Kontrollraum.
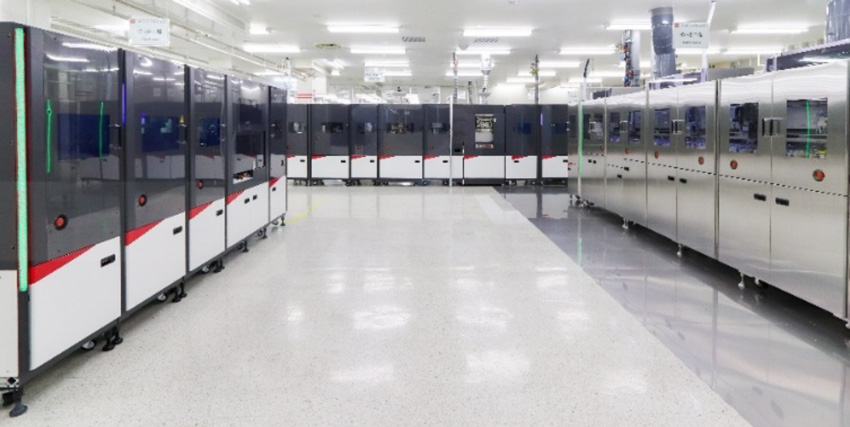
Erste Fertigungslinie [Die Bond → Gate Cut] in der hinteren Bildmitte, mittlere
Fertigungslinie [Deflashing → Plating] auf der rechten Seite, letzte
Fertigungslinie [Mark → Trim and Form] auf der linken Seite
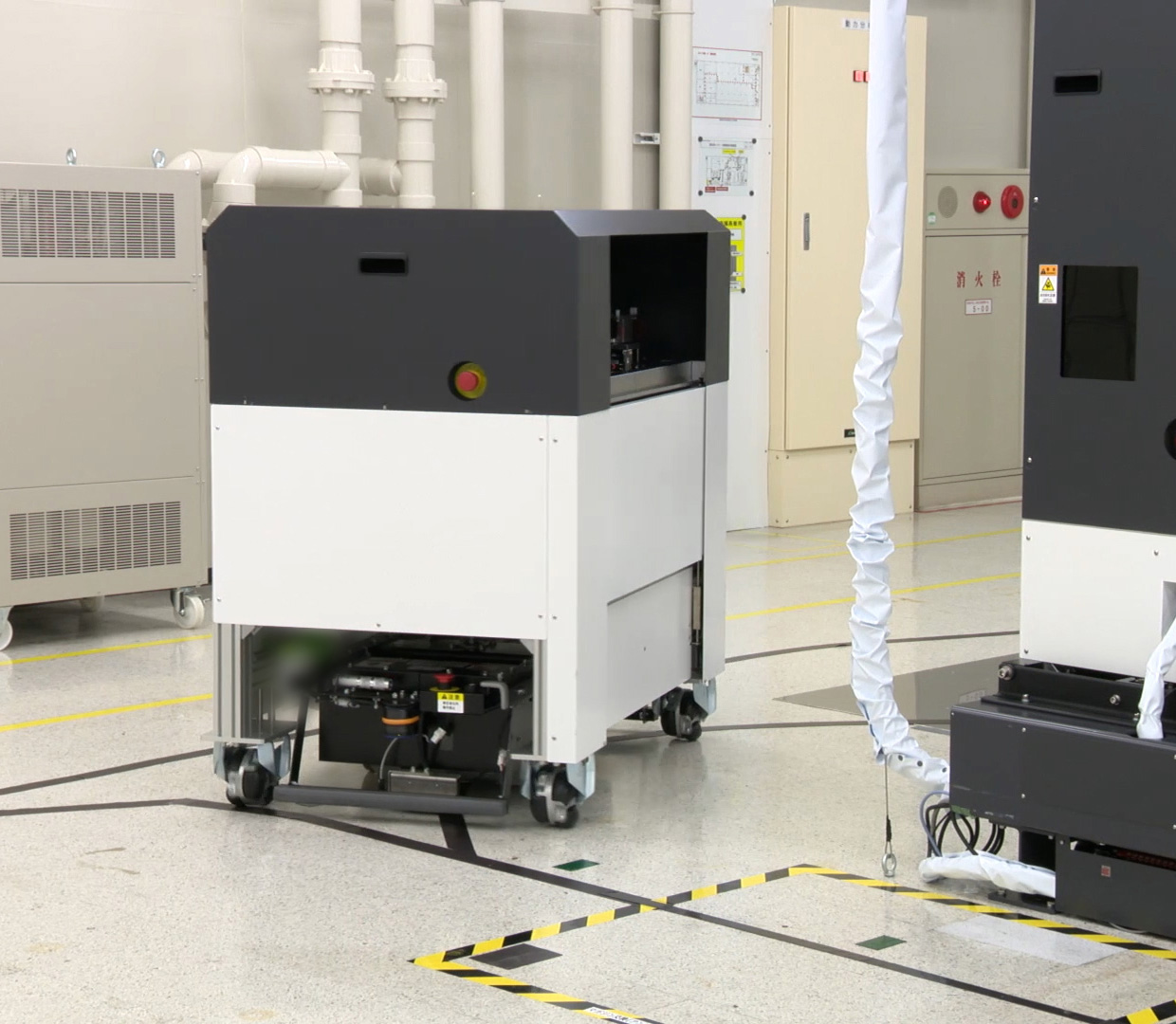
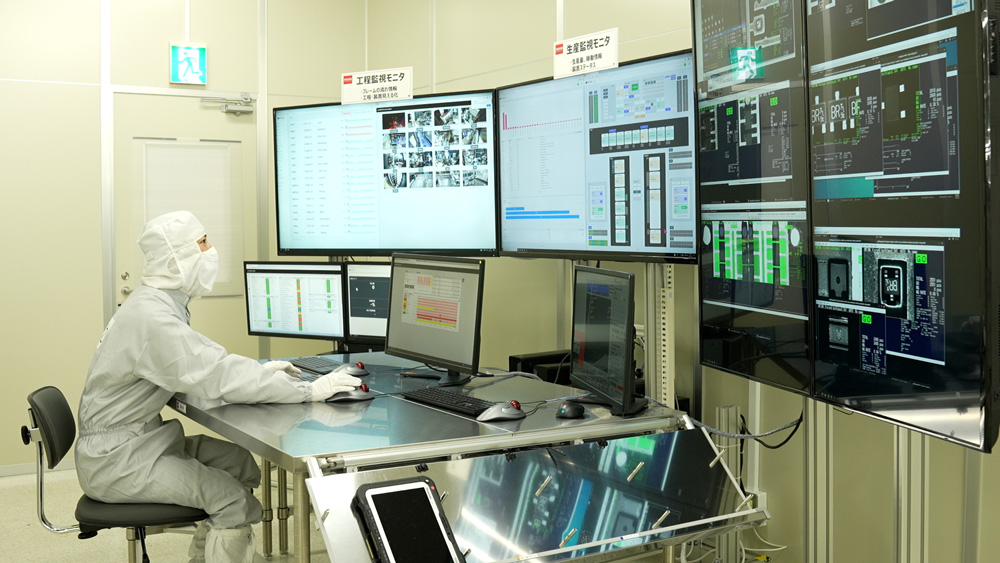
ROHMs Produktionssystem
Seit der Gründung im Jahr 1954 hat ROHM seine eigenen Produktionssysteme entwickelt, was unter Halbleiterherstellern selten ist. Über drei Generationen von Hauptproduktionslinien hinweg, die auf die Back-End-Verarbeitung im Jahr 1980 zurückgehen, haben wir eine Massenproduktion mit verbesserter Qualität und niedrigeren Kosten erreicht.
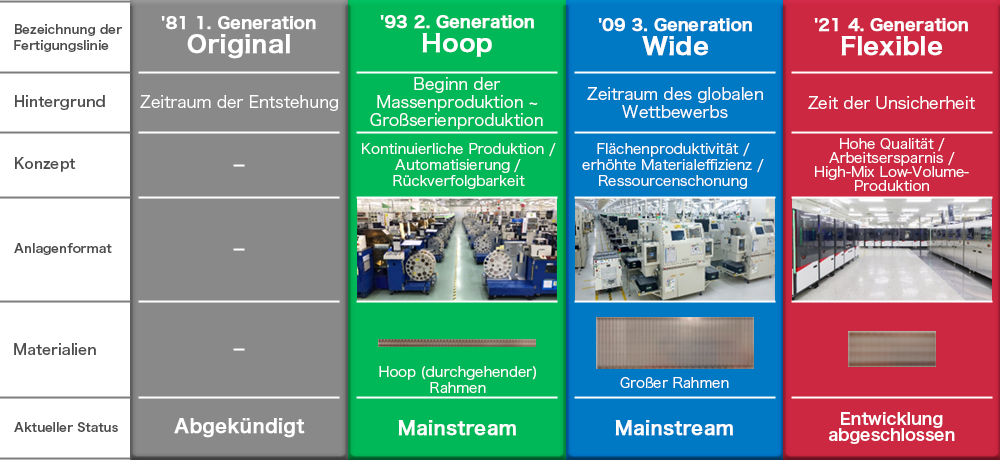
Mr. Miwa, General Manager der Abteilung für Fertigungsinnovation, der sich seit vielen Jahren mit der Konstruktion von Produktionssystemen befasst, spricht über die Entwicklung von Produktionssystemen zur Erfüllung verschiedener Kundenanforderungen sowie über die Wettbewerbsgrundsätze der gesamten Branche gegenüber konkurrierenden Herstellern.
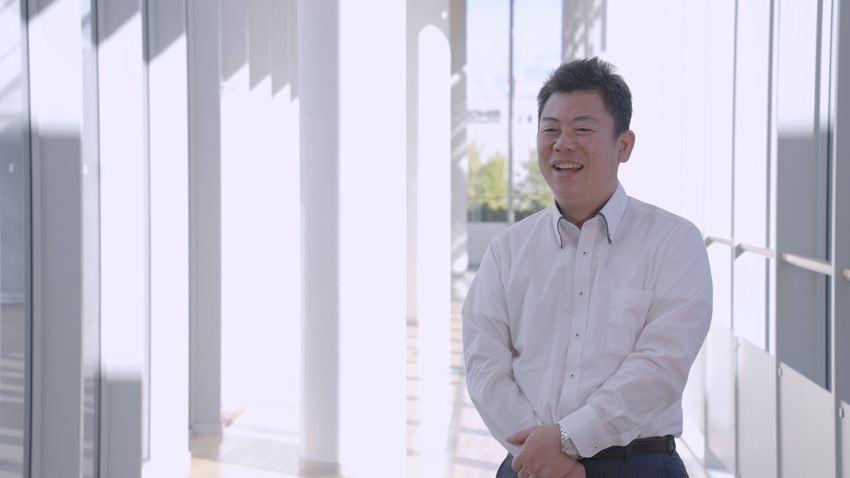
Damals besuchte ich das Werk eines Herstellers mit einer High-Mix High-Volume Produktion. Das war der Ausgangspunkt für die Entwicklung der flexiblen Linie ROHM's.
Das Ziel lautet: Keine Fehler
Miwa:
"Ein weiterer Konflikt war, dass bei einer Vergrößerung des Rahmens zur Steigerung der Produktivität ein bestimmtes Qualitätsniveau nicht mehr erreicht werden konnte. Die Qualitätsanforderungen der Kunden, insbesondere bei Produkten für die Automobilindustrie, werden von Jahr zu Jahr strenger, so dass wir beschlossen, ein Produktionssystem zu entwickeln, das keine fehlerhaften Produkte produziert. Wir haben dieses Projekt mit dem Ziel begonnen, null Fehler zu erreichen".
Es dauerte etwa anderthalb Jahre, bis das Projekt 2018 in vollem Umfang in Betrieb gehen und für die Massenproduktion eingesetzt werden konnte. Neben dem Streben nach Qualität, das von Anfang an ein Hauptziel war, erwies sich der Prozess der Überprüfung unter Berücksichtigung der Anforderungen eines Produktionssystems der nächsten Generation schwieriger als erwartet
Miwa:
"Um ehrlich zu sein, gab es niemanden, der das Konzept verstand, etwas zu schaffen, das völlig anders war als das, was in der Vergangenheit gemacht wurde. Selbst innerhalb des Unternehmens hatten wir Mühe, einen Weg zu finden, um diese optimierten Produktionsmittel voranzutreiben. (lacht)"
Durchdachtes, hochwertiges Design
In Massenproduktionssystemen, wie dem oben beschriebenen Wide-Line-System, wird die Qualität durch die Einführung einer eigenen Prozessvervollständigung zusätzlich zur Sortierung im Endprozess sichergestellt. Bei der Konzeption der flexiblen Linie wagen wir es, die Verarbeitungspunkte zu überprüfen.
Ariga:
"Das von uns entwickelte Konzept besteht darin, die Qualität bereits bei der Verarbeitung einzubeziehen. Um die Qualität in jedem Schritt des Prozesses zu verbessern, haben wir zunächst alle Aspekte in Bezug auf Ausrüstung, Materialien und Arbeitsabläufe überprüft. Der Schlüssel liegt darin, die Variabilität von 5M1U zu minimieren. "
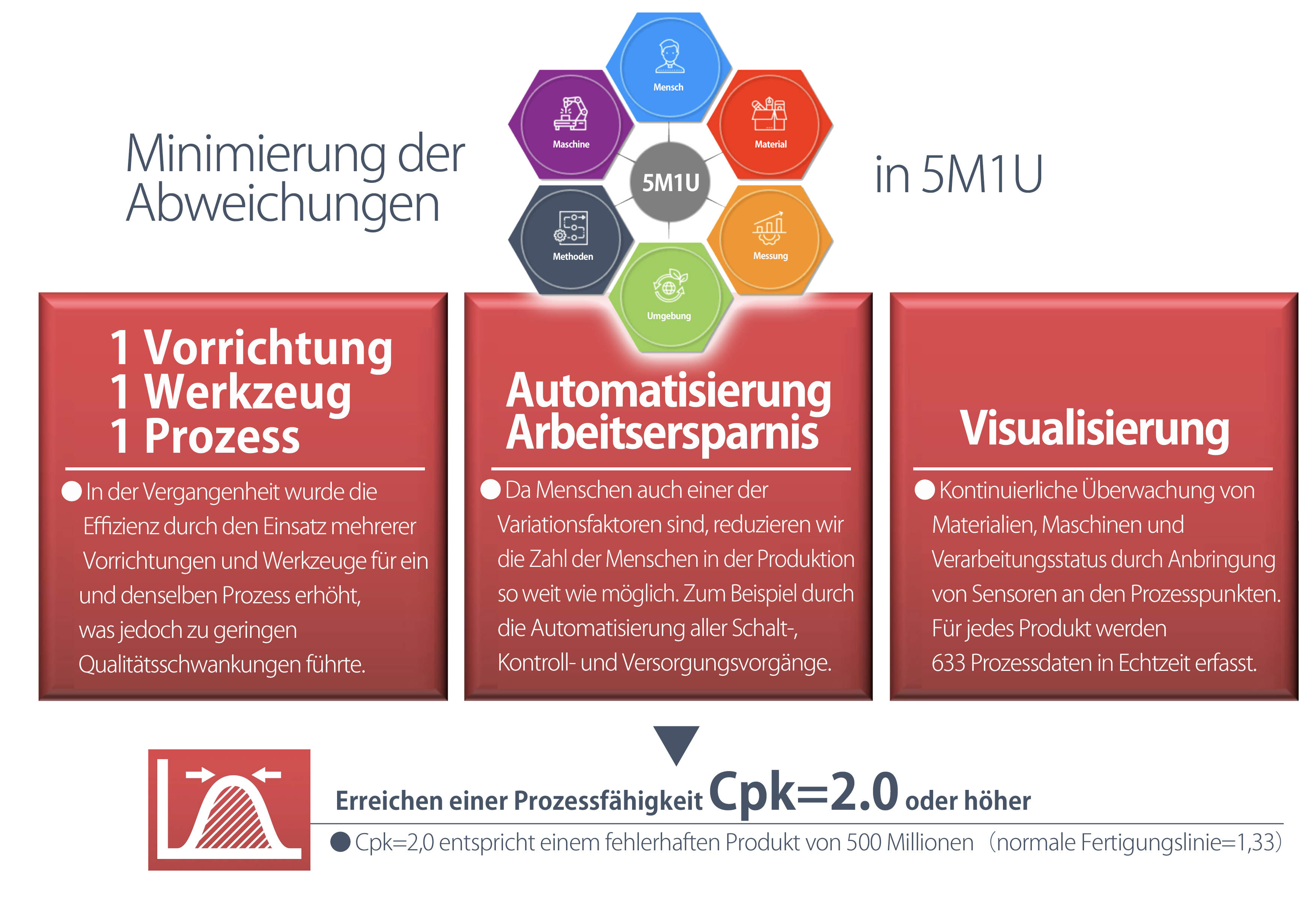
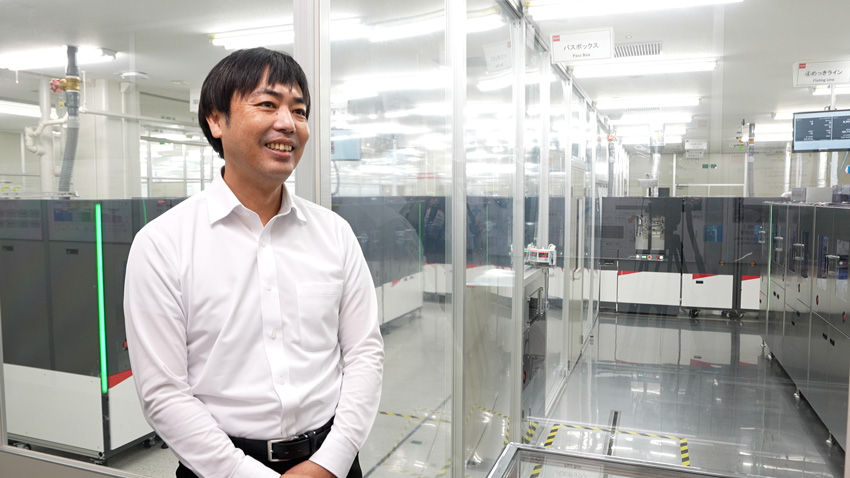
Wir haben einen Bereich eingerichtet, in dem Besucher aus Japan und Übersee sowie angehende Ingenieure und Studenten das Innere des Reinraums besichtigen können.
Die hochmoderne Ausstattung erregt sofort Ihre Aufmerksamkeit.
"Ich bin für eine Reihe von Vorgängen verantwortlich, von der Entwicklung und Inbetriebnahme von Halbleiter-Backend-Fertigungslinien bis zur Überführung in die Massenproduktion. Bis heute haben wir mehr als 100 Anlagen in Fabriken auf der ganzen Welt installiert."
Ariga:
"Bisher haben wir uns in vielen Bereichen auf die Erfahrung und die Intuition von Fachkräften verlassen. Die Quantifizierung der Ergebnisse ermöglicht es uns, erhebliche Vorteile zu erzielen, nicht nur in Bezug auf die Qualität, es können auch verschiedene Probleme vermieden werden, bevor sie auftreten. Und für den unwahrscheinlichen Fall einer Beschwerde durch den Kunden können wir dank der lückenlosen Rückverfolgbarkeit die Ursache in Echtzeit bis hin zum einzelnen Produkt selbst ermitteln."
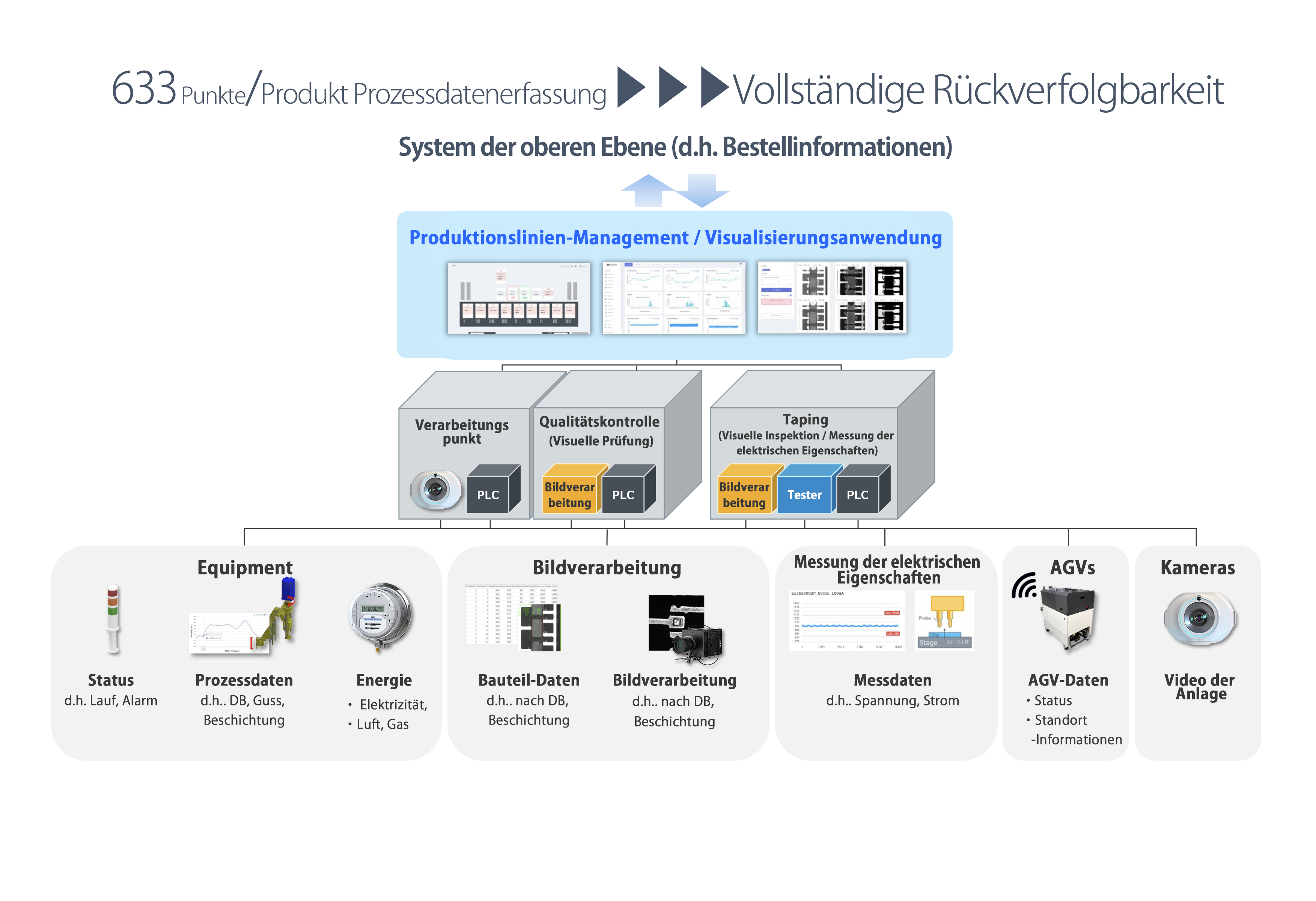
High-Mix-Low-Volume-Produktion
Die flexible Fertigungslinie von ROHM hat ein Potenzial von 4,5 Millionen Stück/Monat bei voller Produktion. Derzeit (ab 2022) stellen wir zwei Transistortypen in Serie her, planen aber in naher Zukunft etwa 10 Modelle in Massenproduktion herzustellen.
Dies ist ein wichtiges Alleinstellungsmerkmal dieser Linie, das durch die bereits erwähnte Vereinfachung des Schaltvorgangs durch Automatisierung ermöglicht wird. Laut General Manager Miwa von der Abteilung für Fertigungsinnovation besteht das grundlegende Konzept in der Herausforderung einer "nicht auf Massenproduktion ausgerichteten Fertigung".
Miwa:
"In einer Branche, in der Massenproduktion und Lagerhaltung die Norm sind, gehen wir zum ersten Mal eine High-Mix-Low-Volume-Produktion an. Das war schon eine Herausforderung für sich. Wir sind davon überzeugt, dass wir eine stabile Versorgung gewährleisten können, indem wir ein kontinuierlich wechselndes Produktionssystem mit einer breiten Linie für große Aufträge und einer flexiblen Linie für kleinere Mengen einrichten."
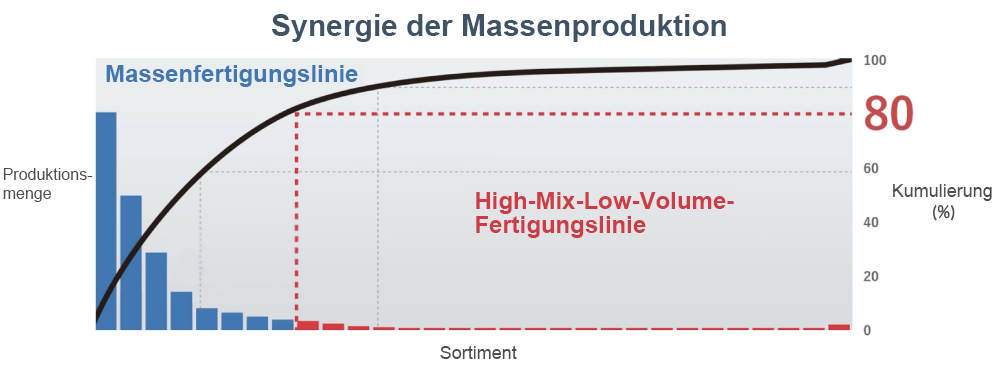
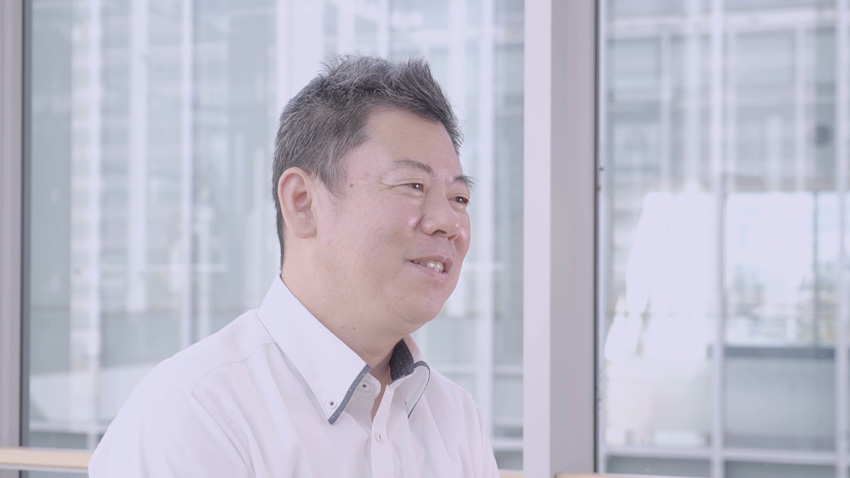
"Was Sie brauchen, wenn Sie es brauchen, nur in der benötigten Menge." ROHM ist sich bewusst, dass viele Kunden, z. B. in der Automobil- und Industriebranche, langfristig und stabil mit kleinen Stückzahlen versorgt werden müssen.
Wir freuen uns, von einem Automobilhersteller, der unsere flexible Anlage besichtigte, zu hören, dass ROHM der einzige Anbieter war, der eine solche Idee hatte und sie umsetzen konnte.
Technologie-Nachfolge mit ONE ROHM
Miwa:
"Da ROHM ein integriertes Produktionssystem hat, halte ich es für wichtig, ein Umfeld zu haben, das eine enge Koordination und einen Meinungsaustausch zwischen den Abteilungen ermöglicht."
Bei der Entwicklung dieser Anlage, die sich von den konventionellen Vorgehensweisen in der Halbleiterindustrie abhebt, war es wichtig, Meinungen aus verschiedenen Perspektiven einzuholen. Gleichzeitig ist ein langfristiges kooperatives System erforderlich, um verschiedene Blickwinkel zu nutzen und den Grad der Fertigstellung zu verbessern, während sich Entwurf/Entwicklung → Prototypenbewertung → Bewertung der Massenproduktion wiederholen.
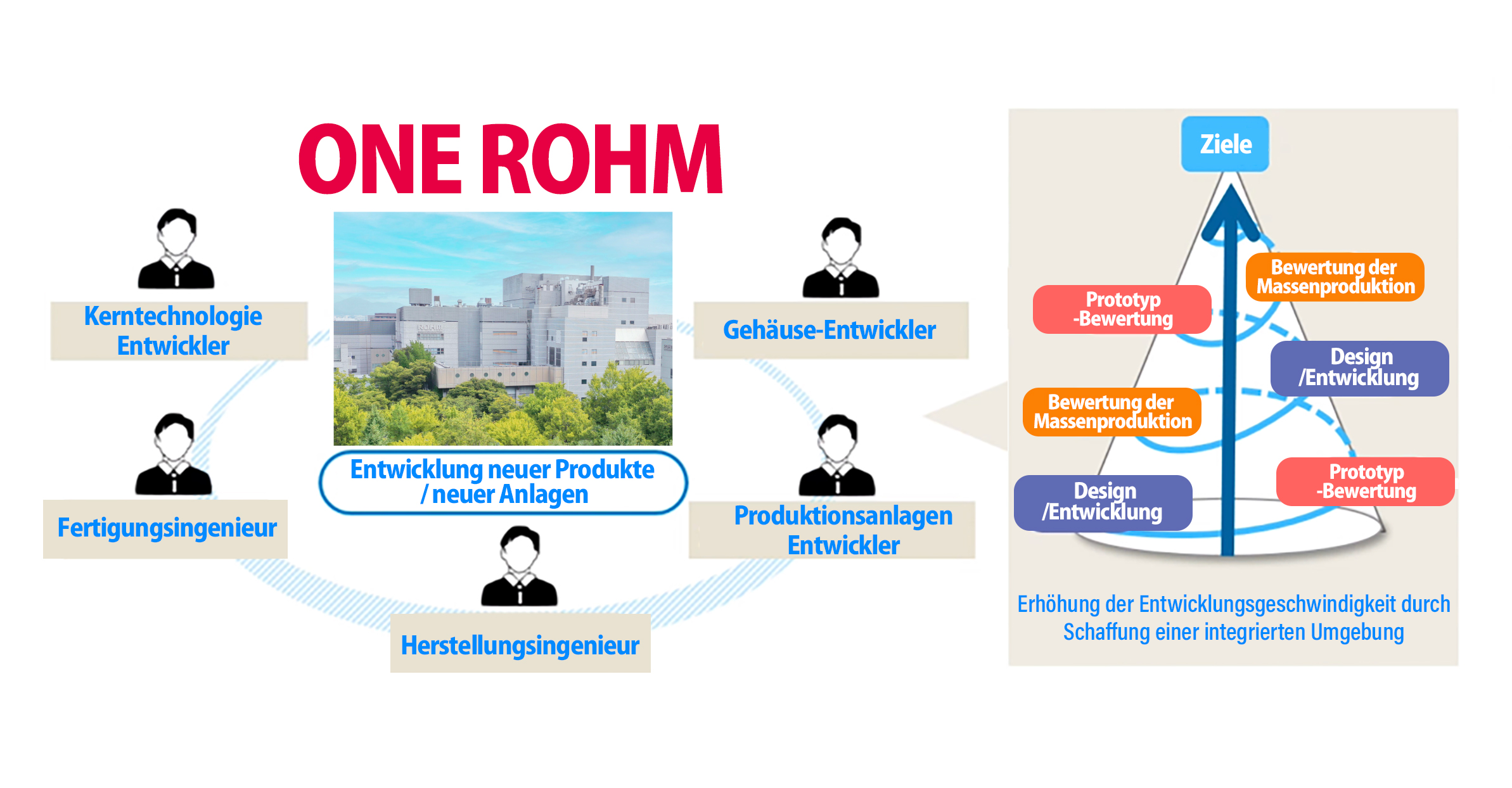
Dank des einzigartigen Umfelds von ROHM mit Spezialisten in jeder Abteilung konnte diese schwierige Aufgabe bewältigt werden.
Miwa:
"Ein weiterer wichtiger Punkt ist das in den letzten 60 Jahren angesammelte Wissen und Know-how. In diesem Sinne kann man sagen, dass die flexible Linie die "Technologie-Nachfolge" von ROHM darstellt."
sagt Mr. Miwa, der die Entwicklungsstelle leitet, wo er mit Begeisterung junge Ingenieure beobachtet und sich mit ihnen austauscht. Horizontale Bindungen, die über Abteilungen hinausgehen, und Wissen und Geisteshaltung, die von Generation zu Generation weitergegeben werden. Indem wir den Wert von ONE ROHM weiter steigern, kann Monozukuri Schritt für Schritt in die Zukunft gehen.
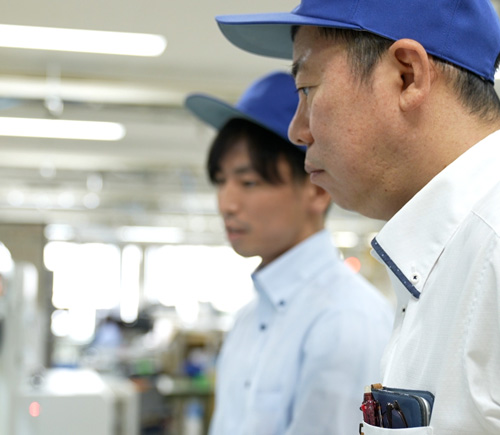
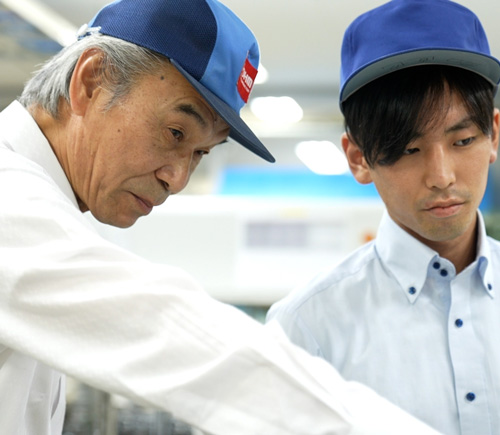
Im Entwicklungszentrum am Hauptsitz in Kyoto werden täglich Entwürfe, Prototypen und Massenproduktionen verschiedener in Japan und im Ausland verwendeter Produktionsanlagen bewertet. Es ist auch ein Ort, an dem junge Ingenieure etwas über Monozukuri (Fertigung) lernen.
BCP / Umweltmaßnahmen
Die Verifizierung der Massenproduktion unserer flexiblen Anlage begann im Jahr 2020. Die Welt befand sich mitten in der COVID-19-Pandemie.
Ich bin mir sicher, dass jeder noch frisch im Gedächtnis hat, dass die Hersteller in der Automobil-, Unterhaltungselektronik-, Haushaltsgeräte- und anderen Industrien gezwungen waren, Maßnahmen zu ergreifen, um mit der Verzögerung bei der Produktion und dem Vertrieb von Halbleitern in der ganzen Welt fertig zu werden.
Seitdem ist das Umfeld der Fertigungsindustrie einem ständigen Wandel unterworfen, einschließlich der fortlaufenden Überprüfung der Produktionsstandorte in Japan, da der Mangel an Halbleitern aufgrund steigender Energiepreise und Naturkatastrophen noch nicht behoben ist. Vor diesem Hintergrund rückt die flexible Linie als effektives Produktionssystem für BCP-Maßnahmen in den Fokus.
Masuda:
"Die flexible Anlage hat einen sehr hohen Automatisierungsgrad, so dass es durch die Installation der exakt gleichen Ausrüstung an mehreren Standorten möglich sein wird, Produkte mit der gleichen Qualität zu jeder Zeit herzustellen.
Ich glaube, dass dies in diesen unsicheren Zeiten unverzichtbar sein wird, wenn es darum geht, unseren Kunden dauerhaft Produkte zu liefern."
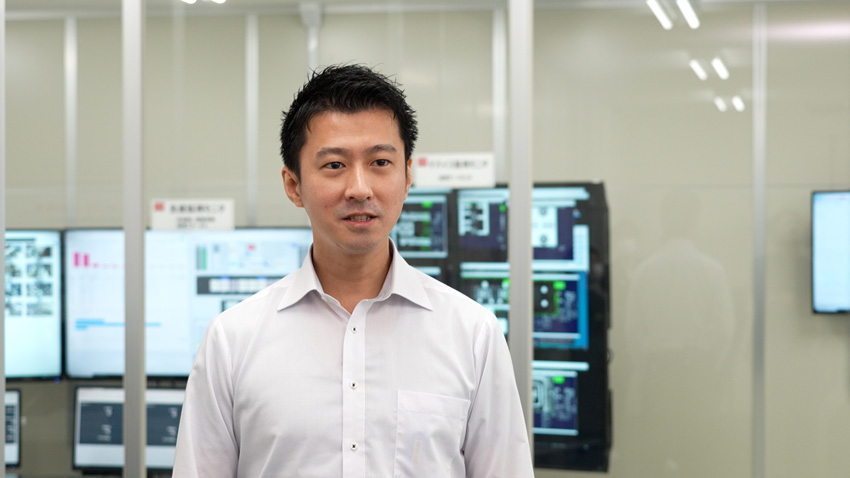
Bereich Entwicklung von Produktionslinien, Abteilung Fertigungsinnovation
Die vollständige Automatisierung und die Reduzierung des Personaleinsatzes führen zu einer Verdoppelung der menschlichen Produktivität im Vergleich zu herkömmlichen Produktionsanlagen. Es wurde eine bemerkenswerte Verringerung der Arbeitsstunden des Bedienpersonals um 87 % errechnet.
"ROHM hat eine Kultur, die uns die Freiheit gibt, Projekte wie dieses in Angriff zu nehmen, bei denen wir nicht wissen, ob wir auf den Füßen landen werden."
Ein weiteres wichtiges Merkmal ist, dass die durch die oben erwähnte "Visualisierung" gesammelten Daten zur kontinuierlichen Veranschaulichung und Überwachung des Energieverbrauchs verwendet werden können. Da der Schutz der Umwelt weltweit zu einem wichtigen Thema wird, bemühen wir uns, die CO2-Emissionen aus der Stromerzeugung zu reduzieren und Energieeinsparungen in der Produktion zu fördern.

(Stadt Hirokawa, Bezirk Yame, Präfektur Fukuoka)
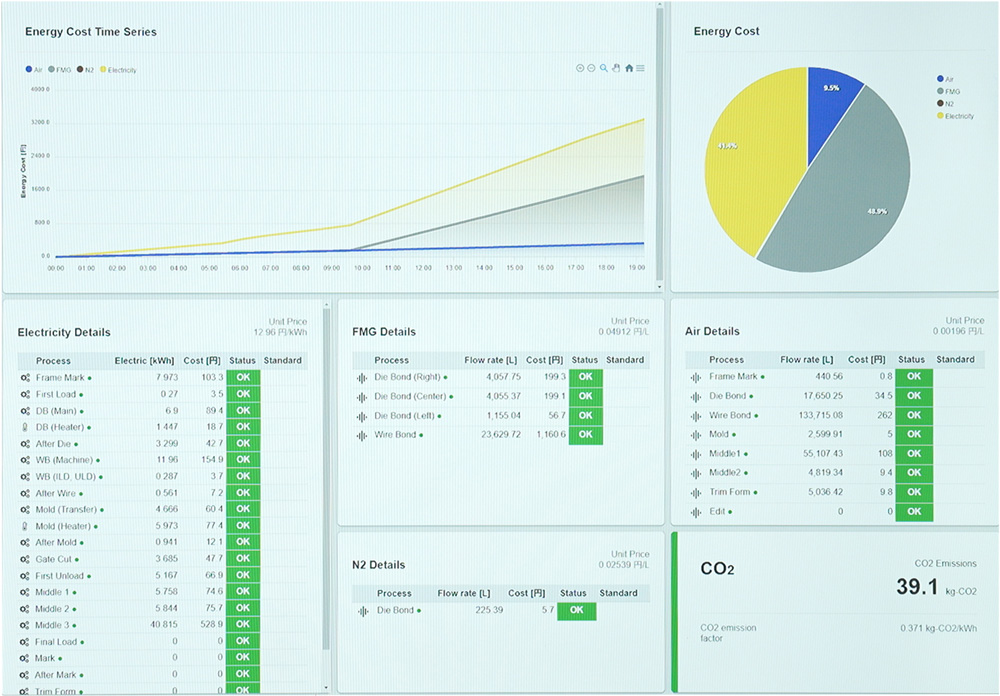
und in CO2-Emissionen umgerechneten Energieverbrauchs
Eine nachhaltige Gesellschaft anstreben...
Eine Zeit, in der die Umweltverträglichkeit der Produktion stark in Frage gestellt wird.
ROHM als Ganzes arbeitet daran, Energie und Ressourcen zu sparen, auch in der Lieferkette.
Eine neue Produktionsplattform
Masuda:
"Wir sind derzeit dabei, verschiedene technische Überprüfungen vorzunehmen, während wir auf dieser Anlage in Serie produzieren. Unsere unmittelbare Aufgabe besteht darin, die hier gewonnenen Element-Technologien auf die nächste Generation von Produktionsanlagen anzuwenden, die wir in Zukunft entwickeln werden."
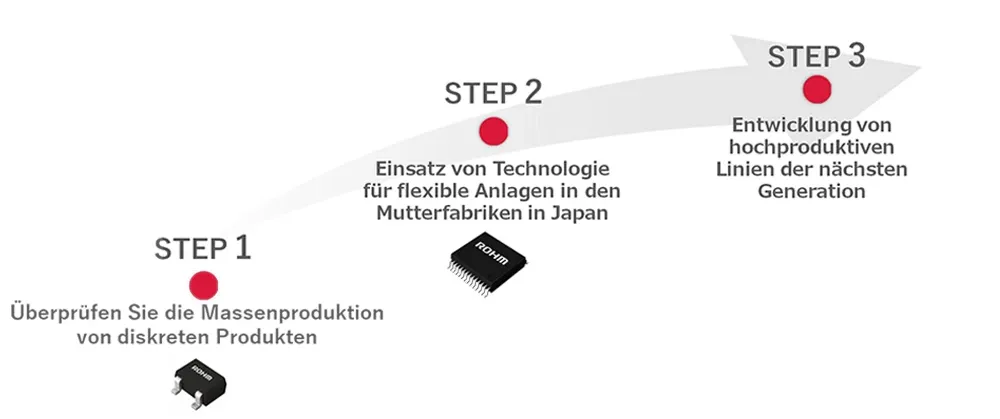
In Zukunft wird diese Technologie im Stammwerk in Japan eingesetzt und die Zahl der im Werk Hirokawa produzierten Modelle erweitert. Wir sind derzeit nicht in der Lage, eine Verschnaufpause einzulegen, bis die unbemannte Großanlage (Massenproduktionsanlage) in den nächsten Jahren fertiggestellt ist. Auf dem Weg zu einer neuen Produktionsplattform, der Kunden auf der ganzen Welt vertrauen. Die Entwicklung und Evolution geht weiter…
Miwa:
Von den 90er bis zu den 2000er Jahren entwickelte ROHM das, was wir Hoop/Wide-Produktionslinien nennen. Diese wurden entwickelt, um eine qualitativ hochwertige Massenproduktion zu niedrigen Kosten zu ermöglichen. Obwohl sie die Hauptproduktionslinien von ROHM bleiben, glauben wir, dass es noch Raum für Verbesserungen in Bezug auf die Verarbeitungsmöglichkeiten, die menschliche Produktivität und die Durchlaufzeit gibt, wodurch wir unseren Konkurrenten immer einen Schritt voraus sind.